STEEL YOUR WEIGHT from worldautosteel on Vimeo.
Advanced High-Strength Steels is the new vehicle lightweighting material. Watch this video to hear automakers, academics and steel engineers explain why it’s the fastest growing material in automotive.
Automotive Weight Reduction and Fuel Consumption, a Complicated Relationship
Automakers’ decisions on materials is an inherent complexity of designing and producing consumer-pleasing automobiles, the trade-offs among a range of competing performance criteria and cost, not to mention demands of stringent government standards. The body structure must contend with extreme demands of multiple and complex loading conditions vital to vehicle handling. Strength, durability and safety are other requirements that the body structure must meet, all of which may impact weight. In other words, it’s complicated. Automakers continue to face these challenges as they strive to achieve the fuel consumption targets.
The Accepted Formula
There is a widely-accepted hypothetical formula that claims a 10 percent reduction in mass can result in a six to eight percent reduction in fuel consumption. But this formula rarely, if ever, occurs in the real world. As a Forschungsgesellschaft Kraftfahrwesen mbH Aachen (fka) study shows, the actual fuel consumption savings depends on factors like driving cycle, vehicle size and powertrain. Powertrain selection has more influence on fuel savings than does weight reduction, especially for urban driving cycles. Further to this point, vehicle manufacturers do not have sufficient engine and powertrain options to apply to every incremental kilogram of weight reduction achieved, and therefore though it is achieved, it does not necessarily mean they can downsize the powertrain. As well, consumers have the option to drive vehicles with smaller, less powerful engines that may be more fuel efficient, but many demand instead to drive larger, more powerful vehicles that accelerate quickly, requiring more fuel.
Mythbuster:
1/3 of One Fill Up Saved?
Per Year?
Two case studies on Light Duty Trucks and Sport Utility vehicles compare aluminium and Advanced High-Strength Steels (AHSS) vehicle versions using the UCSB Automotive Energy & GHG Model (“UCSB Model”). Besides evaluating vehicle total life cycle emissions, the UCSB Model projects fuel consumption savings by considering driving cycles, engines, fuel types, effects of lightweighting, and other factors that impact fuel consumption. In the study, aluminium version was attributed with a 35% mass reduction and AHSS a 25% mass reduction. The UCSB Model results show that fuel consumption was not significantly decreased when substituting aluminium for steel. In other words, this 10% mass reduction over the AHSS version did not equate to the predicted six to eight percent fuel savings. Rather, the data showed that owners of an aluminium-intensive Light Duty Truck could expect to visit the fuel station four less times over the entire life of the vehicle (assuming a 26-gallon tank and 12-year lifetime) than the AHSS-intensive truck owner, or a savings of 1/3 of one fuel fill up per year. The aluminium SUV driver can expect to save about three fill ups at the fuel pump less than steel over the entire vehicle life, or 1/4 of one fuel fill up per year.
Provoked by stiff challenges in the auto industry’s on-going quest for greater fuel efficiency, the steel industry has been aggressively improving its automotive materials for the past 20 years. Automakers are more adventurous than ever in choosing the materials they use to reduce weight, improve fuel economy and lower emissions. As material agnostics, they will use the material best suited to their needs. This demands unrelenting innovation among all material suppliers to deliver high performance and superior value.
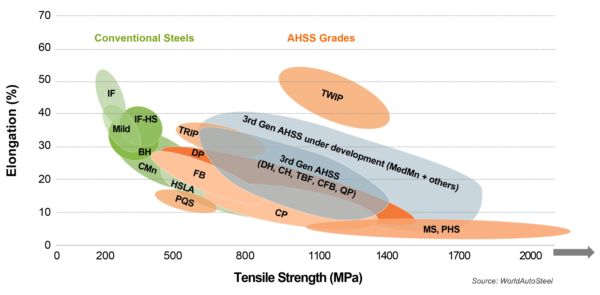
Global Formability Diagram. Unprecedented AHSS strength levels coupled with unique formability (elongation) are matching the formability of conventional mild steels. Steel experts say much more is yet possible in the engineering of new steel grades.
Car makers have responded to steel innovation by incorporating ever-increasing amounts of Advanced High-Strength Steels (AHSS). See our Steel Muscle In New Vehicles section for many examples. These modern grades are fundamental to reducing vehicle mass and emissions, while holding the line on costs. As a result, they are the fastest growing material in light-duty vehicles over the past decade.
Studies commissioned by the steel industry, such as the UltraLight Family of Research and FutureSteelVehicle, spell out new ideas about making structurally efficient steel cars that are still affecting the world of design today. Applying the latest in design optimization techniques, the studies highlight the importance of holistic design — considering the whole vehicle, not just individual parts — and the value of new higher-strength steel grades with properties ideally suited for many vehicle load cases, like frontal crash energy absorption or side-intrusion prevention.
Weight reduction will continue to be relevant with newly designed powertrains, as car manufacturers will be able to reduce battery storage and motor size based on lower mass structures. The choice of material is therefore critical in this respect, and steel will continue to successfully reinvent itself to meet this challenge of weight reduction together with safety and environmental responsibility—at similar costs to conventional steels.